Anti-H2S Corrosion Tubing and Casing
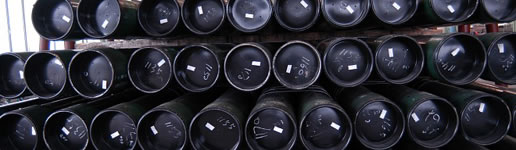
JST H2S corrosion resistance petroleum pipe can be used in corrosion environments with H2S. Currently, about one third of oil and gas wells around the world contain H2S gas. Sichuan, Xinjiang and other oil fields in China all contain H2S gas that can cause stress corrosion cracking tubing and casing and huge loss. This anti-H2S corrosion tubing and casing can be used in the areas with 8% H2S content and can well solve the corrosion fracture problem. H2S corrosion resistance petroleum pipe is characterized by good mechanical properties, impact, hardness and performance to fully meet the technical requirements of users. It is typically used in downhole environments with low content of hydrogen sulfide. This anti-H2S corrosion tubing and casing has been applied in Sichuan, Tarim, Xinjiang Northwest Bureau, the Central Plains, Jianghan Oilfield Shengli and other domestic oilfields. JST H2S corrosion resistance petroleum pipe is also exported to Canada, Kazakhstan and other foreign oil fields.
Advantages1. This product is made of pure steel. We adopt high purity steel smelting technology and vacuum degassing method to make the content of P equal or less than 0.015% while S equal or less than 0.008%. JST also uses calcium treatment technology for this anti-H2S corrosion tubing and casing to control inclusion morphology and five harmful elements.
2. JST H2S corrosion resistance petroleum pipe has stable performance. After quenching, the cross-sectional area of steel pipes can acquire more than 98% martensitic structure. After tempering, it can form small and uniform tempering sorbite structure.
3. This anti-H2S corrosion tubing and casing has resistance to stress corrosion and eliminates residual stress. The surface forms a highly stable corrosion-resistant oxide film with the thickness of one or several atomic layers.
4. JST H2S corrosion resistance petroleum pipe has a uniform structure and even hardness. The grain size is more than Grade 8.
5. The steel is smelt by electric furnace or oxygen blown converter. If customers do not have special requirements, as a supplier, we will determine it and use hot-rolled seamless steel pipes.
6. For the inspection of this anti-H2S corrosion tubing and casing, JST configures full spectrum direct-reading spectrometer, Japan metallurgical microscope, impact testing machine, tensile testing machine, computer controlled electro-hydraulic servo universal testing machine and a variety of machine tools. Metal specimen of H2S corrosion resistance petroleum pipe does stretching, flaring, squashing, curling and other physical properties tests. JST can also do sulfide stress corrosion cracking (SSC) test to ensure stable performance of this anti-H2S corrosion tubing and casing.
7. Our proprietary grades allow us to offer the best solutions for each customer’s specific well conditions.
8. Through the JST global network of manufacturing facilities and threading shops, we are able to ensure flexible delivery terms and an outstanding ability to respond to changes in the operation of H2S corrosion resistance petroleum pipe.
9.JST anti-H2S corrosion tubing and casing is manufactured to the most exacting quality standards. We hold a global ISO 9001 registration for our operations, which follow a uniform quality policy and apply a rigorous quality management system.
10. We can supply H2S corrosion resistance petroleum pipe in bare, uncoated condition or with OD/ID coatings such as bitumastic and coal tar epoxy coatings.ClassificationThe resistance to H2S stress corrosion of this anti-H2S corrosion tubing and casing can meet the requirements of NACE 0177 standards.
- JST General H2S Corrosion Resistance Petroleum Pipe
It includes JST80S, JST90S, JST95S and JST110S. The H2S stress corrosion performance of JST80S, JST90S and JST95S is that they will not crack in H2S ‘A’ saturated solution with the load of SMYS×85% after 720 hours. The H2S stress corrosion performance of JST110S is that it will not crack in H2S ‘A’ saturated solution with the load of SMYS×80% after 720 hours.
2. JST H2S High Anti-H2S corrosion tubing and casing
This kind of H2S corrosion resistance petroleum pipe includes JST80SS, JST90SS, JST95SS and JST110SS. The H2S stress corrosion performance of JST80SS, JST90SS and JST95SS is that they will not crack in H2S ‘A’ saturated solution with the load of SMYS×90% after 720 hours. The H2S stress corrosion performance of JST110SS is that it will not crack in H2S ‘A’ saturated solution with the load of SMYS×85% after 720 hours.
Grade | Model | Max. or Tolerance Range (wt %) | |||||||||
C | Mn | Si | P | S | Cr | Mo | Ti | Cu | Ni | ||
80 | JST80S | 0.30 | 0.90 | 0.35 | 0.015 | 0.008 | 0.90 | 0.50 | 0.05 | 0.20 | 0.20 |
JST80SS | |||||||||||
90 | JST90S | 0.30 | 0.90 | 0.35 | 0.015 | 0.008 | 1.20 | 0.50 | 0.05 | 0.20 | 0.20 |
JST90SS | |||||||||||
95 | JST95S | 0.30 | 0.90 | 0.35 | 0.015 | 0.008 | 1.20 | 0.50 | 0.05 | 0.20 | 0.20 |
JST95SS | |||||||||||
110 | JST110S | 0.30 | 0.90 | 0.35 | 0.015 | 0.008 | 1.20 | 0.50 | 0.05 | 0.20 | 0.20 |
JST110SS |
Grade | Yield Strength (MPa) | Tensile Strength (MPa) | Hardness | Elongation | Impact Toughness | ||
Rt0.5 a | Rm | ||||||
Min | Max | Min | HRC | HBW | |||
JST80S | 552 | 655 | 655 | 23 | 241 | Calculate according to API 5CT formulas. | According to API 5CT requirements |
JST80SS | 552 | 655 | 655 | 23 | 241 | ||
JST90S | 621 | 724 | 689 | 25.4 | 255 | ||
JST90SS | 621 | 724 | 689 | 25.4 | 255 | ||
JST95S | 655 | 758 | 724 | 25.4 | 255 | ||
JST95SS | 655 | 758 | 724 | 25.4 | 255 | ||
JST110S | 758 | 862 | 800 | 30 | 294 | ||
JST110SS | 758 | 862 | 800 | 30 | 294 |
Technical Parameters Parameters of this anti-H2S corrosion tubing and casing refer to the excel table.
Recommend Selection Principles1.If the partial pressure is more than 100KPa and the volume ratio is over 5%, we choose SS grade H2S corrosion resistance petroleum pipe.
2. If the partial pressure is between 0.34 KPa and 100 KPa and the volume ratio is from 0.01% to 5%, we choose S grade anti-H2S corrosion tubing and casing.
3. If the partial pressure is less than 0.34 KPa and the volume ratio less than 0.01%, we select non sulfur resistance grade H2S corrosion resistance petroleum pipe.
Certificate In 2011, we obtained the test report from Sichuan Petroleum Administration Acidic Oil and Gas Field Material Corrosion Detection Assessment Center.
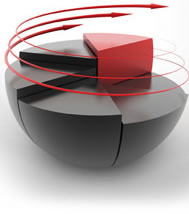
- Home
- About Us
- - Group Overview
- - Company Profile
- - Brand Development Path
- - FAQ
- - R&D Strength
- - Project Achievements
- - Why choose us
- - Download
- News
- Products
- API 5L Line Pipe
- - Onshore Line pipe
- - Offshore Line pipe
- - Through Flowline(TFL)
- - PSL-2 Line Pipe Applied in Marine
- - Acid Corrosion Resistant PSL-2 Line Pipe
- - PSL-2 Sour Service Line Pipe
- - DNV ABS LR API Line Pipe
- - X52 X60 X70 X80 QS Line Pipe
- - Coating of Line Pipe
- API 5CT
- - API 5CT Series Coupling
- - API 5CT Series Tubing
- - API 5CT Series Casing
- - API 5CT Coupling Stock
- - API 5CT Pup Joint
- JST Special Series of Tubing and Casing
- - Perforating Gun Pipe
- - Collapse Resistant Casing
- - Ultra High-Strength Casing
- - 3Cr Corrosion Resistant Tubing & Casing
- - Anti-H2S Corrosion Tubing
- - CO2 Corrosion Resistant Tubing
- - Low Temperature Service Tubing and Casing
- - Heavy Oil Thermal Pipe
- - Premium Connection
- API 5DP Drill Pipe
- Anticorrosion Steel Pipe
- International Standard
- - ASTM/ASME Standard
- - EN Standard
- - DIN Standard
- - JIS Standard
- Steel Tube Applications
- Steel Tube Process
- Quality
- - Certificates
- - Production Process
- - Online Test
- - Physical and Chemical Test
- - Quality Assurance
- - Technical Services
- - After Service
- - Cost Savings
- Views
- - Cooperation and Communication
- - Steel-Making Mill
- - Tube-Making Mill
- - Tube Processing Mill
- - Heat Treatment Mill
- - Online Test
- - Physical and Chemical Test
- - Key Equipment
- - Products Details
- - Higher Steel Grade Product
- - Packaging and Transportation
- - Warehouse & Inventory
- Environment
- - Training
- - Work in JST
- Careers
- Contact Us